Underwater Die Face Resurfacing
Premature wear on small underwater pelletizing blades is a common industry issue. In our experience, often the problem is caused by breakdown of the die rather than a failure of the blade itself.
Continuous use wears down pelletizing die surfaces, leading to the formation of grooves. Smooth die faces are crucial to prevent unpredictable start-up and uneven knife wear. Worn die extrusion holes develop rounded edges, resulting in tails and inconsistent pellet quality.
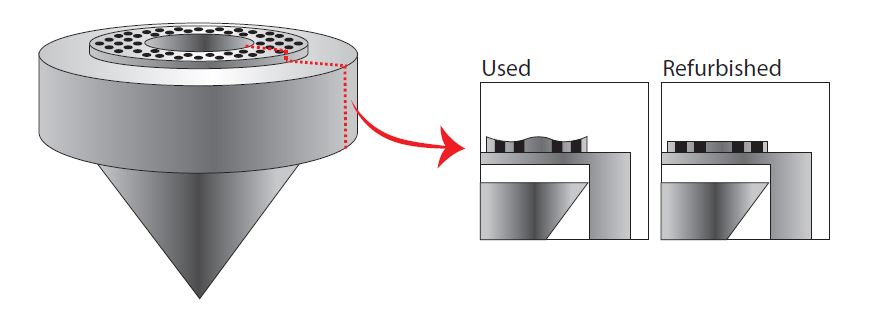
Remove Imperfections to save time, improve throughput, and save on blade costs. Generally, if you can feel an imperfection on the surface of your die, it needs to be reconditioned.
Die Services
- Die Replacement
- Dieface Replacement
- Dieface Grinding
Performance Engineered Metallurgy
- Wc Tungsten carbide wear surface material
- TiC Titanium carbide Ferro-tic® wear surface material
- Stellite® wear surface material
- Inconel 625
Contact Our Team
Leverage our decades of experience to solve your strand pelletizer feed roll challenges.
Advantages of Reconditioning the Die Surface
- Faster start up
- Elimination of tails
- Increased production
- Improved pellet consistency
- Knives wear evenly
- Reduction of metal particles in the steam
- Increased knife life
- Increased up time
Why Choose Great Lakes Industrial Knife?
Industry Expertise
With decades of experience in rotor manufacturing, we understand the challenges of pelletizing and offer solutions that meet the highest standards of performance and reliability.
Customer-Centric Approach
We work closely with our customers to understand their unique needs and provide tailored solutions that enhance their operational efficiency and productivity.
Made in the USA
Our skilled machinists and engineers can produce or repair all types of bolt-on, wedge lock, solid head helical pelletizer rotors and bed knives right here in the USA, which reduces lead times and transportation costs.
Stellite® is a registered trademark of Deloro Stellite Company Inc.
Ferro-TiC® is a registered trademark of Pacific Sintered Metals
CPM 10V®, CPM M4® are registered trademarks of Crucible Materials Corp.